Fasteners and Machining: Customized Solutions for every single Production Demand
Fasteners and Machining: Customized Solutions for every single Production Demand
Blog Article
Navigating the Globe of Fasteners and Machining: Strategies for Accuracy and Rate
In the detailed world of fasteners and machining, the mission for precision and speed is a perpetual challenge that demands precise interest to information and strategic preparation. From recognizing the varied array of fastener types to picking ideal materials that can stand up to strenuous needs, each action in the process plays a critical role in attaining the desired outcome.
Understanding Bolt Kind
When picking bolts for a job, comprehending the various kinds readily available is critical for ensuring optimum efficiency and dependability. Fasteners come in a variety of kinds, each developed for specific applications and needs. Screws are utilized with nuts to hold materials with each other, while screws are functional fasteners that can be made use of with or without a nut, depending upon the application. Nuts, on the various other hand, are internally threaded fasteners that friend with screws or screws, providing a safe and secure hold. Washers are crucial for dispersing the tons of the fastener and protecting against damage to the product being secured. Additionally, rivets are irreversible bolts that are perfect for applications where disassembly is not needed. Comprehending the distinctions between these fastener types is essential for picking the right one for the work, ensuring that the connection is solid, durable, and reliable. By selecting the ideal bolt kind, you can maximize the efficiency and longevity of your task - Fasteners and Machining.
Choosing the Right Materials
Understanding the value of choosing the ideal products is paramount in making sure the ideal performance and dependability of the chosen fastener kinds reviewed formerly. When it involves bolts and machining applications, the product option plays an important duty in identifying the total stamina, longevity, corrosion resistance, and compatibility with the designated environment. Various materials supply varying residential properties that can substantially influence the performance of the fasteners.
Common materials made use of for bolts include steel, stainless steel, brass, aluminum, and titanium, each having its one-of-a-kind toughness and weak points. Steel is renowned for its high stamina and longevity, making it ideal for a broad variety of applications. Selecting the ideal material involves thinking about variables such as stamina needs, environmental problems, and budget plan restrictions to guarantee the wanted efficiency and long life of the fasteners.
Precision Machining Techniques
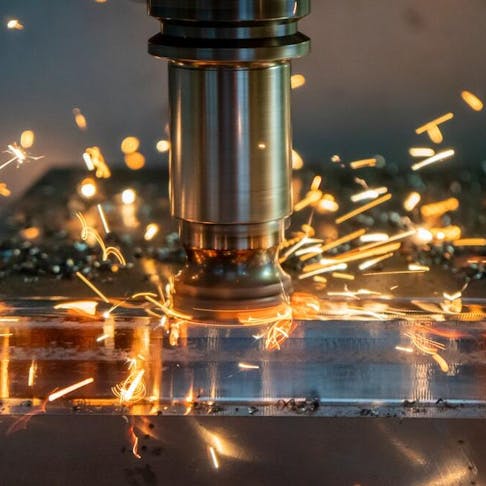
In addition to CNC machining, various other precision methods like grinding, turning, milling, and exploration play essential duties in fastener manufacturing. Grinding helps attain great surface area finishes and limited dimensional resistances, while transforming is frequently utilized to produce round elements with exact sizes. Milling and drilling operations are vital for forming and producing openings in bolts, guaranteeing they meet precise specifications and feature appropriately.
Enhancing Speed and Performance
To maximize bolt manufacturing processes, it is necessary to streamline operations and execute reliable techniques that complement accuracy machining techniques. One crucial technique for boosting rate and efficiency is the implementation of lean production concepts. By reducing waste and concentrating on continual enhancement, lean techniques help get rid of traffic jams and enhance operations. Additionally, spending in automation modern technologies can dramatically improve manufacturing rate. Automated systems can deal with repeated jobs with precision and speed, allowing employees to concentrate on more complex and value-added tasks. Adopting Just-In-Time (JIT) supply management can additionally improve effectiveness by guaranteeing that the right materials are readily available at the correct time, reducing excess stock and minimizing preparations. Moreover, fostering a culture of partnership and interaction amongst group members can enhance overall effectiveness by advertising openness, problem-solving, and technology. By incorporating these methods, producers can attain an equilibrium between speed and precision, ultimately boosting their affordable edge in the fastener industry.
High Quality Control Actions
Carrying out strenuous top quality control steps is important in guaranteeing the reliability and uniformity of fastener products in the manufacturing process. Quality control measures include numerous phases, beginning with the selection of basic materials to the final examination of the finished bolts. One essential facet of top quality control is performing weblink complete material inspections to validate conformity with requirements. This entails examining variables such as material durability, composition, and strength to ensure that the fasteners satisfy market standards. Additionally, keeping an eye on the machining processes is important to promote dimensional accuracy and surface area coating quality. Using sophisticated innovation, such as computerized inspection systems and precision measuring devices, can improve the precision and efficiency of high quality control procedures.
Regular calibration of equipment and equipment is critical to maintain consistency in production and make sure that bolts fulfill the needed resistances. Applying rigorous procedures for determining and resolving problems or non-conformities is important in protecting against substandard products from getting in the market. By establishing a detailed top quality control structure, manufacturers can copyright the reputation of their brand name and deliver bolts that fulfill the greatest criteria of performance and toughness.
Verdict
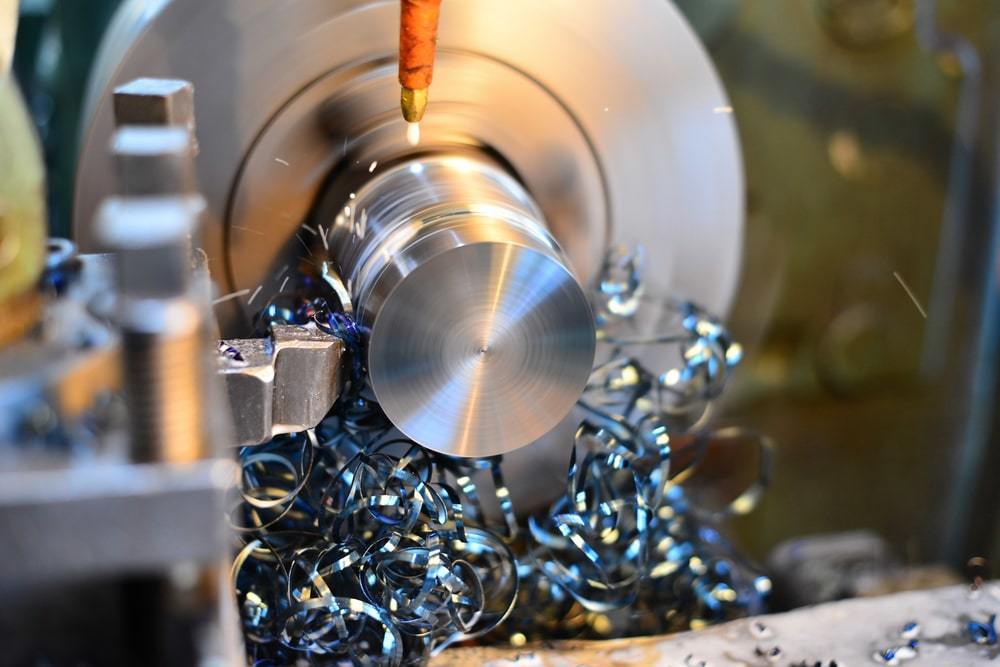
In the intricate realm of bolts and machining, the mission for accuracy and rate is a perpetual obstacle that demands thorough focus to information and calculated preparation. When it comes to bolts and machining applications, the product option plays an essential function in identifying the general toughness, durability, corrosion resistance, and compatibility with the intended setting. Precision machining includes various innovative techniques that ensure the limited resistances and requirements required for bolts.In enhancement additional reading to CNC machining, various other precision techniques like grinding, turning, milling, and boring play crucial roles in fastener production.To optimize bolt production processes, it is essential to streamline operations and execute efficient methods that Discover More Here complement accuracy machining strategies.
Report this page